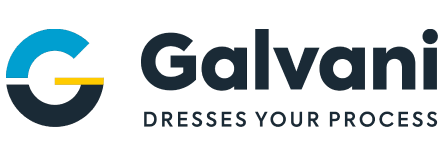
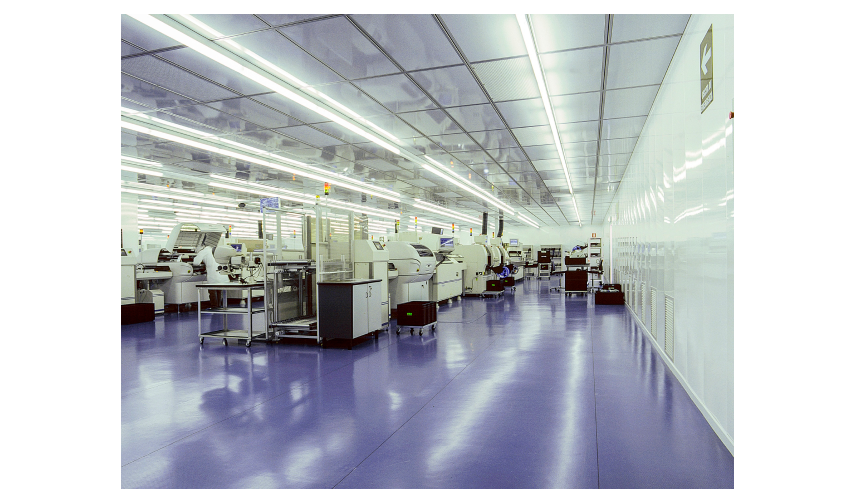
Galvani
Clean rooms, clean rooms, dry rooms, BSL laboratories, beverage solutions
EXPERTS IN CLEAN ROOMS, LAMINAR FLOW SYSTEMS AND CONTROLLED CONTAMINATION ENVIRONMENTS
In the world of clean rooms, Galvani is a true institution: for more than 30 years, the clean rooms of the Verona-based company, together with its solutions for companies that need to produce in contamination-controlled environments and its systems for air distribution and contamination control, have been chosen by giants from all over the world, from Nestlé to Coca Cola, from Luxottica to Safran.
Find out more about the brand
Galvani is always informed about the increasingly stringent international regulations on cleanliness, hygiene, safety and quality; on the basis of these requirements, it develops technologies and systems aimed at guaranteeing the best customised product, tailor-made for its customers. It does not limit itself to design: it even takes care of the construction of the components in its own mechanical workshops, together with installation by its own qualified technicians. They are in fact true turnkey proposals, accompanied by a qualified after-sales service, scheduled maintenance and remote assistance.
ALL GALVANI SOLUTIONS
From false ceilings to doors, from absolute filters to walls, Galvani Cleanrooms boast the highest quality materials and of course comply with the most stringent ISO standards. Direct production is part of the secret of its products: by studying, designing and manufacturing them all in its own workshops, the Veronese company is able to guarantee maximum process and product safety, the highest levels of performance, UNI EN ISO 9001:2015 certified production, full compliance with European quality standards and compliance with international regulations on cleanliness, safety and environmental protection.
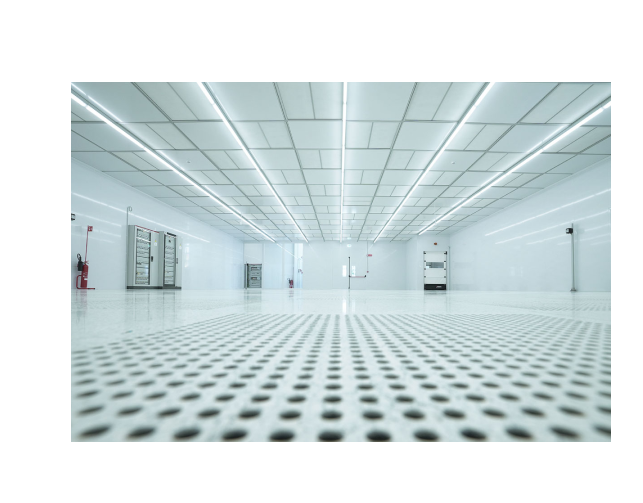
The clean room consists of a closed environment with controlled contamination characterized by very pure air with a very low presence of suspended dust microparticles (from 10,000 to 50,000 times cleaner than normal air) thanks to the presence of special filtration systems. Usually used for mechanical, medical, food, electronic or chemical processing, this chamber is also characterized by temperature, humidity and pressure kept constantly under control, essential conditions for activities and processing where a sterile, aseptic and monitored environment is needed. Galvani is the only company in Italy that directly produces the necessary components, offering a unique, personalized service, immediately ready for use and of the highest quality.
Particularly necessary for companies in the pharmaceutical, medical and food sectors, these rooms are indispensable in all those contexts where the presence of “life” (e.g. germs, bacteria, microorganisms, viruses) can be dangerous. This specific contamination differentiates it from clean rooms. During the care and observation of certain patients or in the case of pharmaceutical, food and beverage production activities, a similar level of cleaning and sterilization is necessary, unlike in different fields (e.g. microelectronics, optics, aerospace, semiconductors) where clean rooms already offer the necessary control of the amount of particles suspended in the air. The sterile room is microbiologically controlled thanks to the use of the most sophisticated chemical sterilization systems, microbial tests and bacterial load analysis.
Dry environment ideal for certain types of processing, where the relative humidity rate is below 5%, a characteristic that differentiates it from the clean room (the relative humidity level here ranges from 40 to 60%). In fact, in some production contexts, it is not enough to just deal with contamination, but it is also necessary to keep the temperature and, above all, the humidity rate under control. An example of this is the development and production of lithium batteries, which must necessarily be protected from the risk of corrosion, together with other activities related to the microelectronics and automotive sectors. Dry Rooms, like clean rooms, are also equipped with air contamination control systems (particles per m³), temperature and pressure.
Also known as “PCL Laboratories” (Phisical Containment Laboratories), they are controlled environments, designed to allow the safe handling of infectious materials; as potentially dangerous pathogens, they require specific containment systems so that operators and the external environment are exposed as little as possible or not at all to these agents. They are differentiated based on risk groups of pathogens, the classification of which occurs based on infectivity, individual and collective transmissibility, pathogenicity, host spectrum and neutralizability. There are four levels of containment: BSL 1 in case of low risk (individual and collective) of infectious agents in the processed materials; BLS2 in the presence of material with moderate risk infectious agents; BSL 3 for material with infectious agents potentially transmissible by air (e.g. pathogens that can cause serious illnesses), with high risk at an individual level and moderate risk at a collective level. BSL 4 is the highest level: it refers to the presence of material with dangerous infectious agents, transmissible by air, with high risk, including pathogens that can cause potentially lethal diseases, for which there are no therapeutic measures or vaccines.
The Galvani range was created to provide assistance regarding the emergency of avoiding contamination also in the world of beverage production. The solutions in question are: aseptic rooms and cabins, ventilation units and flushed covers, UltraClean cabins. To delimit, pressurize and decontaminate the process areas of the filling machines from the airborne articulated tank, Galvani suggests flowed covers as the simplest solution, made to measure and equipped with ventilation units and possibly a dedicated lighting system. Controlled contamination cabins (up to ISO class 5) UltraClean have special ventilation, suction, filtration and control systems to keep the parameters of flow rate, temperature, pressure and environmental cleanliness class constant. The bottling process (milk, soft drinks, isotonic drinks) is carried out in the aseptic room, thanks to maximum air cleanliness and special differential pressure/depression parameters which guarantee constant air temperature and humidity. In the aseptic cabinets, there are sophisticated ventilation and extraction systems to ensure maximum protection of drinks from airborne contaminants.
Are you interested in Galvani?
Request information without obligation. By filling in the form, you will immediately have access to the general presentation of the brand to learn in detail how its technologies work. You can also select other brands to receive further information.